Sistema de dosagem de gases corrosivos – Kit de instalação
Poluentes na atmosfera, como dióxido de enxofre, ácido sulfídrico, dióxido de azoto ou cloro, podem causar danos corrosivos consideráveis a materiais, componentes, conjuntos, dispositivos e edifícios. Os testes de gases corrosivos são cruciais nas áreas de investigação, conceção e garantia de qualidade, a fim de avaliar a adequação e a fiabilidade dos materiais para aplicações específicas e de evitar falhas por corrosão. Para garantir resultados comparáveis, estes testes são realizados em conformidade com diferentes normas de teste. Os sofisticados sistemas de testes de corrosão são, assim, essenciais para a investigação sistemática de padrões de corrosão (suscetibilidade à corrosão/resistência à corrosão).
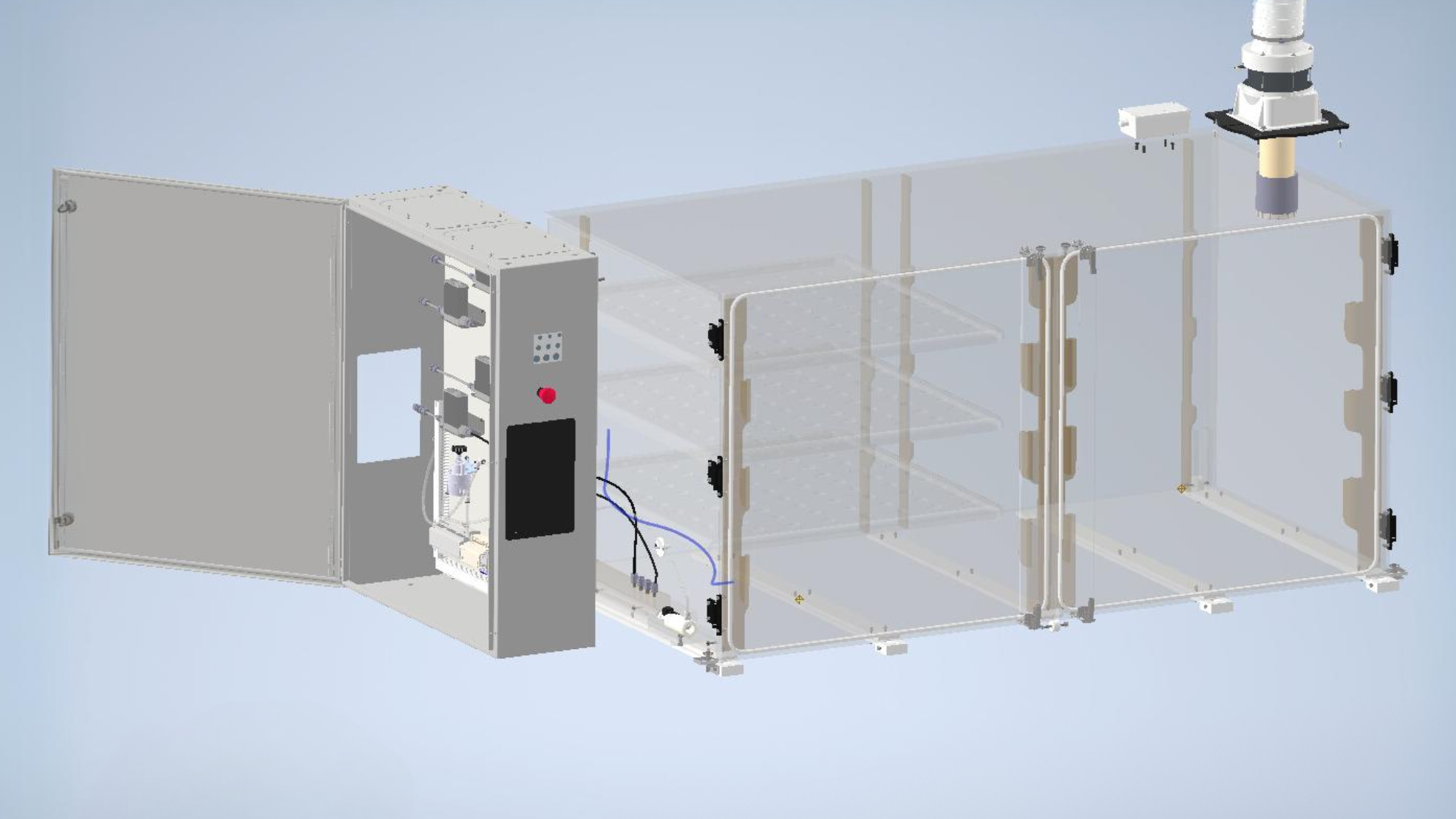
Sistema único de dosagem de gases corrosivos
Com base na nossa vasta experiência em olfatometria dinâmica e na experiência resultante em mistura e diluição de gases, desenvolvemos um sistema único de dosagem de gases corrosivos.
Este sistema permite uma regulação extremamente precisa da dosagem de gases corrosivos, mesmo em concentrações muito baixas, e simultaneamente garante uma mistura homogénea ideal dos gases corrosivos com o gás transportador.
Esquema do nosso sistema de dosagem de gases corrosivos
Exemplo: IEC 60068-2-60 Ensaio de corrosão com fluxo de gás misto
Software de utilizador especialmente desenvolvido
Ao mesmo tempo, desenvolvemos um software de utilizador especialmente concebido para o guiar ao longo de todos os processos padronizados – totalmente seguro e descomplicado.
Este software proporciona uma interface de utilizador intuitiva que o guia passo a passo ao longo de todo o processo do teste de corrosão. Isto otimiza o seu fluxo de trabalho e aumenta a sua eficiência.
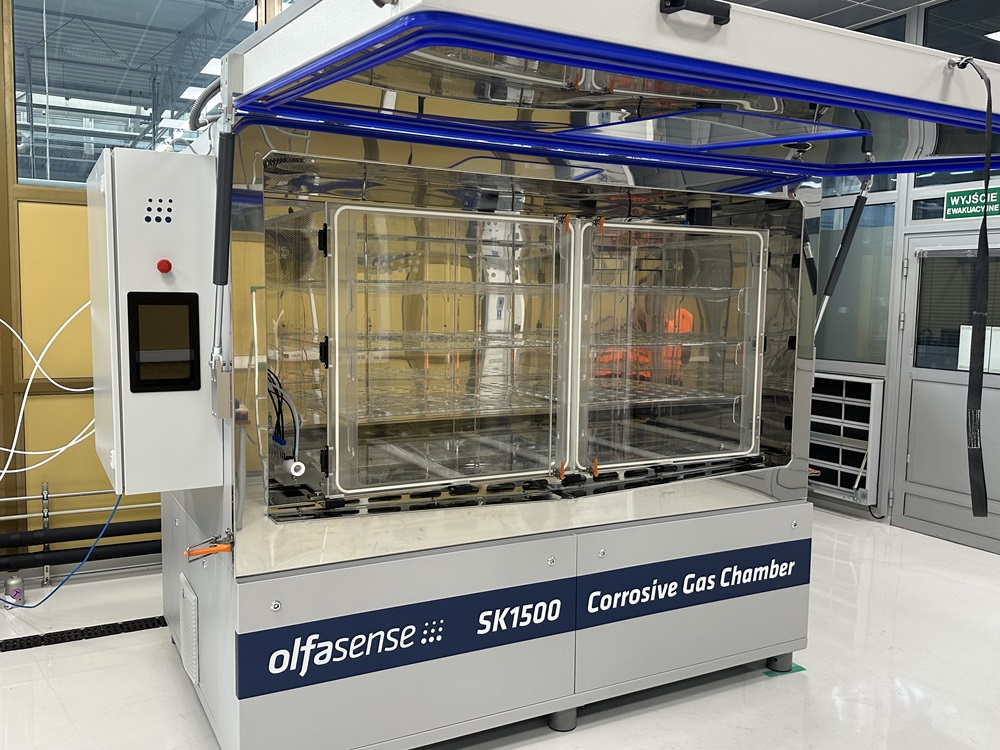
O nosso sistema de dosagem de gases adapta-se a câmaras climáticas de todos os tamanhos
O nosso sistema de dosagem de gases corrosivos pode ser facilmente adaptado e integrado em diferentes câmaras climáticas de vários tamanhos e também pode ser perfeitamente integrado em câmaras climáticas existentes. Se tem uma câmara climática mais antiga que já não usa, temos a solução perfeita para si. Podemos personalizar e integrar o nosso sistema de dosagem de gases corrosivos de última geração na sua câmara. Assim poupará dinheiro e aumentará a usabilidade da sua câmara, pois a caixa de PMMA também pode ser removida, deixando a sua câmara climática disponível para novas medições.
Graças a esta adaptabilidade, temos a capacidade de lhe oferecer soluções extremamente versáteis que podem ser personalizadas com precisão, de acordo com as suas necessidades específicas e as condições de uma ampla variedade de ambientes de teste. Entre em contacto connosco para saber mais sobre esta opção eficiente e rentável.
Características principais
- Resultados ideais graças à dosagem de gases corrosivos de alta precisão com recurso a um controlador de fluxo de massa de alta qualidade.
- Injeção ideal dos gases corrosivos no jato livre do gás transportador e homogeneização por expansão do difusor antes da entrada na câmara de ensaios. Como consequência, mesmo as concentrações mais baixas na ordem de 10 ppb misturam-se de forma homogénea e são introduzidas na câmara de ensaios na concentração especificada.
- Monitorização contínua das taxas de renovação do ar e das concentrações de gás de acordo com três parâmetros independentes, com desligamento automático quando os parâmetros do processo são ultrapassados. Entre estes, o registo e o controlo da pressão interna da câmara de ensaios, a taxa de entrada do ar transportador, a taxa de fornecimento de ar da dosagem de gás corrosivo e as características do ventilador em relação à velocidade.
- Regulação da taxa de renovação do ar através de um sensor de fluxo na entrada da câmara de ensaios de gases corrosivos. Isto garante concentrações corretas de acordo com a norma correspondente quando os gases corrosivos entram na câmara de ensaios, evitando que as concentrações ultrapassem o valor padrão.
- Software especialmente desenvolvido para a aplicação de testes de gases corrosivos, que guia o utilizador, de forma intuitiva, ao longo das etapas individuais do processo.
- Visão clara do material de teste graças às janelas de vidro acrílico de alta qualidade (polimetacrilato de metilo) que proporcionam um meio de observação transparente.
- Conformidade com as normas de teste líderes do setor, como IEC 60068-2-60, IEC 60068-2-42/43 e outras, para garantir resultados de teste confiáveis.
Características de desempenho
- Gases passíveis de testes: ácido sulfídrico (H2S), dióxido de enxofre (SO2), cloro (Cl2) com gás transportador N2, dióxido de azoto (NO2) com gás transportador de ar sintético e outros
- Dosagem de até quatro gases corrosivos com 4 linhas de dosagem de gases corrosivos entre 1-100 ml/min
- Um dispositivo de segurança integrado monitoriza a pressão para um funcionamento sem falhas
- Ligação para recolha de amostras de gás para análise posterior
- Possibilidade de testar a concentração de gases corrosivos com ar seco ou nitrogénio